Jeder kennt es, jeder schloss es innig in sein Herz: Das BIG Bobby Car aus Kunststoff mit weißem Lenkrad begleitete schon viele Menschen durch ihre Kindheit. Voller Freude sausten sie querbeet über asphaltierte Spielstraßen und Hinterhöfe, fuhren steile Abhänge hinab und meisterten selbst schwierige Kurven. Dass nur die Beine als Antriebselement zur Fortbewegung dienten, spielte keine Rolle – das Gefühl allein zählte.
Doch das Wissen, aus welcher Hand das beliebte, nahezu unzerstörbare Fahrspielzeug eigentlich stammt und wie es angefertigt wird, kann heutzutage angesichts der Flut von Plastikartikeln ausländischer Produzenten auf dem Markt leicht in Vergessenheit geraten.
Dabei trägt der Hersteller BIG, inzwischen ein Tochterunternehmen der Simba Dickie Group, das Markenzeichen „Made in Germany“ zu Recht und ist ein waschechtes Stück deutscher Erfolgsgeschichte. Ein kleiner Blick in den Produktionsprozess verrät die Geheimnisse, die hinter dem Ferrari für Kleinkinder stehen.
Ein neuer Anfang
Im Jahr 1972 stellte BIG erstmalig unter der Führung von Ernst A. Bettag das BIG Bobby Car öffentlich vor und legte damit den Grundstein für eine Spielzeuglegende. Seit dieser Zeit mauserte sich das BIG Bobby Car nicht nur zu einem der meist geliebten Rutschfahrzeuge, sondern wandelte sich außerdem fast zu einem Synonym für Unverwüstlichkeit. Diese markante Qualität schien auch dem Hersteller eigen zu sein, als dieser sich 1998 nach einem Großbrand der Produktionsstätte in Fürth aufgrund einer defekten Lampe in einer Rekordzeit von nur 16 Monaten erholte. Heute befindet sich das BIG-Spielzeugwerk am Standort Burghaslach, wo täglich große Mengen des roten Flitzers das Fließband verlassen. Nicht zu übersehen, ist auch das gigantische Abbild eines Bobby Cars (8 x 4 x 2,80 m) mit einer Tonne Gewicht auf dem 32.000 Quadratkilometer großen Firmengelände – ein Statussymbol, Danksagung und Würdigung gleichermaßen.
Die Polyethylen-Granulat-Gießerei
BIG gehört zu den modernsten Produktionsstätten Deutschlands überhaupt und greift für die millionenfache Anfertigung seines international geschätzten Sortimentes auf die Unterstützung komplexer Maschinen zurück. Der Hauptbestandteil nahezu aller Produkte, darunter auch zahlreiche Variationen in Form von Traktoren, Bauarbeiterfahrzeugen oder einfachen Sandkästen, ist ein äußerst belastbarer Kunststoff.
Das Polyethylen-Granulat liegt anfangs noch in Form farbloser, kleiner Kügelchen in großen, silbernen Vorratssilos vor. Durch Ansaugpumpen werden diese zu ihrem ersten Bearbeitungsprozess durch ein zentrales Verteilungssystem geführt. Zuallererst noch das Wichtigste: Bevor es durch Hitze und Luftdruck mit Extrusion und Gussverfahren zur Sache geht, steht noch die Einfärbung zum charakteristischen Bobby-Car-Rot an. Direkt im Anschluss zerschmilzt der Kunststoff unter dem Einfluss von 200° Celsius zu einer zähflüssigen Masse.
Für jedes Spielzeug gibt es eine eigene Blaupause in Gussform, in der das aufgeweichte Polyethylen als elastischer Schlauch eingeführt wird. Mittels Druckluft eines starken, mechanischen Gebläses dehnt sich der Stoff nach und nach aus und schmiegt sich auf diese Weise an die vorgegebene Figur an. Gerade einmal eine Minute verstreicht während der ganzen Verarbeitung.
Sengende Flammen putzen das BIG Bobby Car fein heraus
Mächtige Robotergreifarme befördern die noch grobschlächtige Hülle zu ihrer nächsten Station und führen sie dabei durch reinigendes Feuer. Große Brenner, die gleichzeitig von mehreren Seiten arbeiten, verleihen der Oberfläche einen feinen Schliff und säubern es von Überresten sowie scharfen Unebenheiten. Ein absolut notwendiger Vorgang, da grobe Kanten und Splitter ansonsten die Eignung für Kleinkinder zunichtemachen würden, was kaum mit der Firmenphilosophie in Einklang zu bringen wäre.
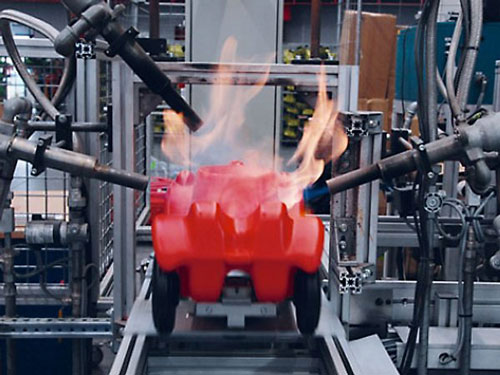
Auf weiteren Fließbändern folgt dann die Montage zusätzlicher Elemente wie Lenkrad und Reifen. Damit auch die beigelegten Sticker während turbulenter Autofahrten nicht den Halt verlieren, wird das nun fast fertig gestellte Bobby Car erneut einer Hitzebehandlung unterzogen.
Nun steht alles bereit für den letzten Schritt: In passender Verpackung tritt der taufrische Raser per LKW die Reise in örtliche Geschäfte und Lagerstätten für den Versandhandel an – bis irgendwann in nahender Zukunft ein staunendes, glückliches Kind sein erstes BIG Bobby Car in Empfang nimmt.
Nachhaltiges Herstellerverfahren mit hohen Sicherheitsansprüchen
Sicherheit für den Nachwuchs ist stets das oberste Gebot. Aus diesem Grund unterzieht sich der Produzent regelmäßigen Prüfungen durch den TÜV, um die Unbedenklichkeit seiner Miniaturfahrzeuge mit Hilfe des GS-Zertifikates zu belegen. Fragwürdige Inhaltsstoffe und schädliche Weichmacher, die durch Hautkontakt oder Lecken in den Körper von Kindern zu gelangen drohen, sollen so möglichst von der Produktion ausgeschlossen werden.
Der verwendete Kunststoff verfügt über eine hohe Elastizität bei gleichzeitiger Stabilität. Gefährliche Brüche, Splitter durch Unfälle oder gar Beulen aufgrund allzu rabiater Fahrtechniken auf der Rennbahn sind so extrem unwahrscheinlich. Wechselwirkungen durch Umwelteinflüsse wie Regenwasser oder intensive Sonneneinstrahlung fallen ebenfalls weg.
Der absolute Clou: Abfälle durch Ausschussware entstehen bei dem angewendeten Fertigungsprozess kaum. Treten unerwartet Mängel trotz der mehrfachen sowie gründlichen Bearbeitung am BIG Bobby Car auf, wird aussortiertes Material durch Rückführung hin zu den Anfängen des Produktionszyklus‘ effizient wiederverwertet. Schredder zerkleinern dabei das feste Gehäuse, während die Beimischung kleiner Mengen frischen Granulats die Konsistenz der beworbenen Materialeigenschaften gewährleistet.